Flachgehäuse aus Holz mit einfachen Mitteln selbst herstellen
Meine Vorliebe gilt Gehäusen aus Holz, weil Holz einfach leichter zu bearbeiten ist als Metall. Gerade bei Versuchsaufbauten, wo ständig umgebaut wird, es dies ein Vorteil. Für ansprechende Gehäuse reicht einfaches Werkzeug aus und der Selbstbau eines Kleingehäuses für die Elekronik wird zum Kinderspiel.
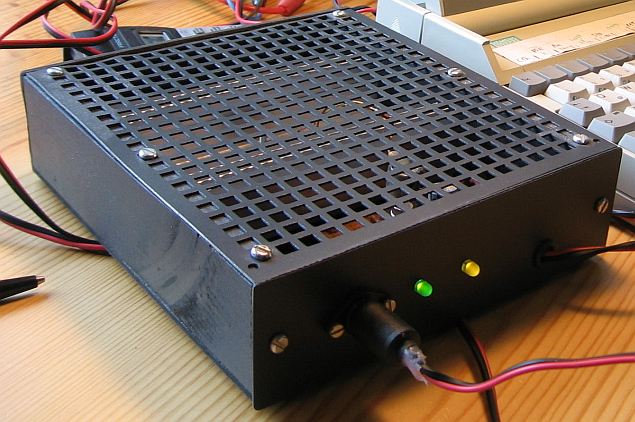
Hätte ich die Seitenteile ordentlich geschliffen und mehrfach lackiert, würde man die Holzmaserung nicht mehr sehen. Der große Vorteil dieser Konstruktion ist, dass man für eine nachträgliche Bearbeitung das Gehäuse bequem auseinanderschrauben kann. Zum Beispiel ist es leicht eine neue Frontplatte zu gestalten. Platinenmaterial eignet sich deshalb für die Frontplatte besonders gut, weil es sich nicht wie Blech bei der Bearbeitung verbiegt. Einen Netztransformator kann man oft gut an das Seitenteil schrauben. Die Schraubenköpfe müssen dann versenkt werden.
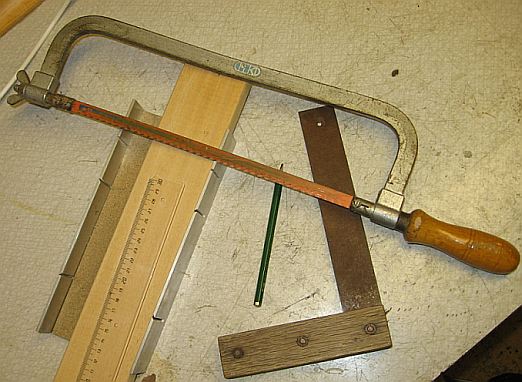
Mit Stichsägen erreicht man diese Genauigkeit selten. Optimal wäre eine kleine Kreissäge, die ich aber nicht habe.
Als Boden oder Deckel verwende ich auch eine Art Presspappe, die einseitig beschichtet ist und für Rückwände billiger Regale und Schränke verwendet werden. Man findet sie auf jeden Sperrmüll. Der Clou ist, dass man dieses Material brechen kann. Dazu muss man das Material beidseitig anritzen, wie es unter Brechen statt Sägen beschrieben ist. Man erhält dann kerzengerade Bruchkanten. Sollten Boden und Deckel nicht genügend Steifigkeit besitzen, kann man die Stabilität mit dünnen Holzeisten erhöhen, die man innen mit Heißkleber aufklebt. Zur Zierde kann man Aluminiumprofile oben und unten an der Front und Rückseite kleben.
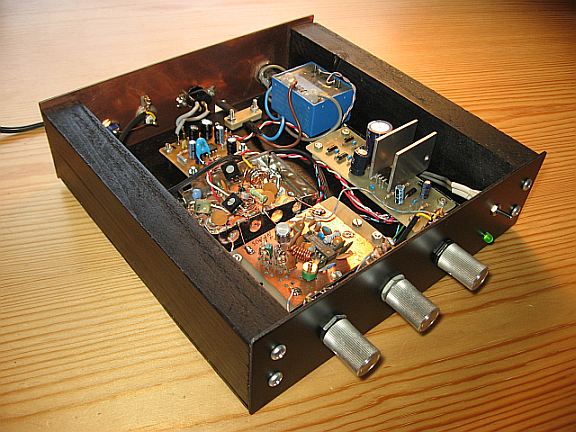
Den Trafo habe ich mit Sekundenkleber befestigt. Abgesehen von den Seitenteilen braucht man also nichts sägen, wenn man statt des Sperrholzes Kunststoffplatten verwendet.
Und hier noch die Unterseite, damit man sieht, wie die Leiterplatten mit M3-Schrauben und Unterlegscheiben befestigt wurden:
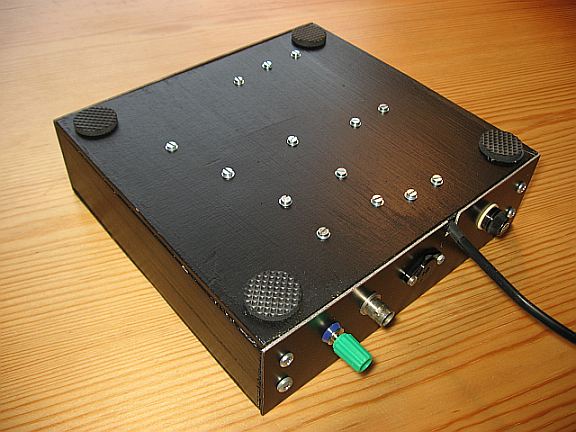
Der Boden gewinnt durch die montierten Leiterplatten zusätzlich an Steifigkeit. Die kleinen Fehler in der Lackierung sind durch Silikonkleber entstanden, mit denen ich die Latten befestigte. Deshalb lieber Holzleim verwenden. Die Gummifüße sorgen nicht nur für Rutschfestigkeit, sondern Verhindern auch ein Zerkratzen der Möbel durch die herausragenden Schraubenköpfe.