16. März 2021 (aktualisiert am 18. und 19. März 2021)
Mit einfachen Werkzeugen lassen sich für Hobbyprojekte Frontplatten aus Aluminium- oder Stahlblech herstellen. Ich gebe wegen der leichteren Verarbeitung und des Aussehens Aluminium den Vorzug.
Als Bleche kommen vorwiegend solche vom Schrottplatz oder aus alten Geräten zum Einsatz. Oft eignen sich Rückwände. Sehr gut lassen sich Bleche aus alten PC-Gehäusen gewinnen.
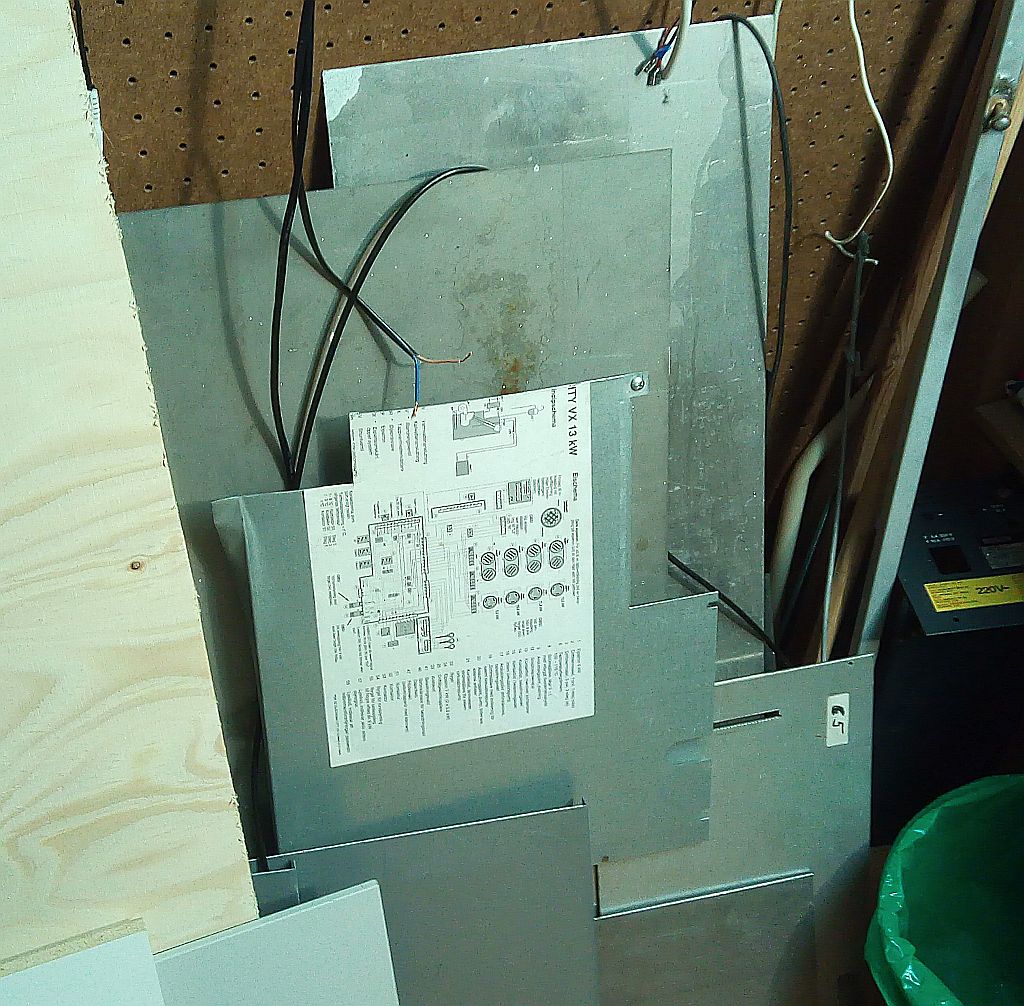
Folgende Werkzeuge werden benötigt: Durchlauf- oder Pelikanblechschere, Hammer, Ständerbohrmaschine oder Bohrmaschine mit Ständer, Holzbrettchen als Unterlage beim Bohren, Schutzbrille für das Bohren, eventuell Lesebrille für das Einzeichnen und Körnen, ein Satz Spiralbohrer, Feilen, Schlüsselfeilensatz, Schieblehre, rechter Winkel mit Anschlag, Knabberzange (meine ist von adelnibbler.com), konische Handreibahle, Körner, dünner Filzstift, Lineal, Geodreieck, eventuell ein Zirkel, feines Schleifpapier, Staubsauger oder Handfeger zum gründlichen Beseitigen der Metallspäne und ein alter Lappen für die abschließende Reinigung der Oberfläche und für den Stofffetzentrick zum Bohren in dünne Bleche.
Praktisch sind auch Stufenschälbohrer, die ich aber noch nicht besitze. Die klassische aber mühsame Art wäre der Einsatz eines Laubsägebogens mit runden Laubsägeblättern für Metall. In Verbindung mit einem Schlüsselfeilensatz lässt sich mit viel Zeit nahezu jede Aufgabe bewältigen. Dann gibt es noch Lochstanzen, die aber teuer sind.
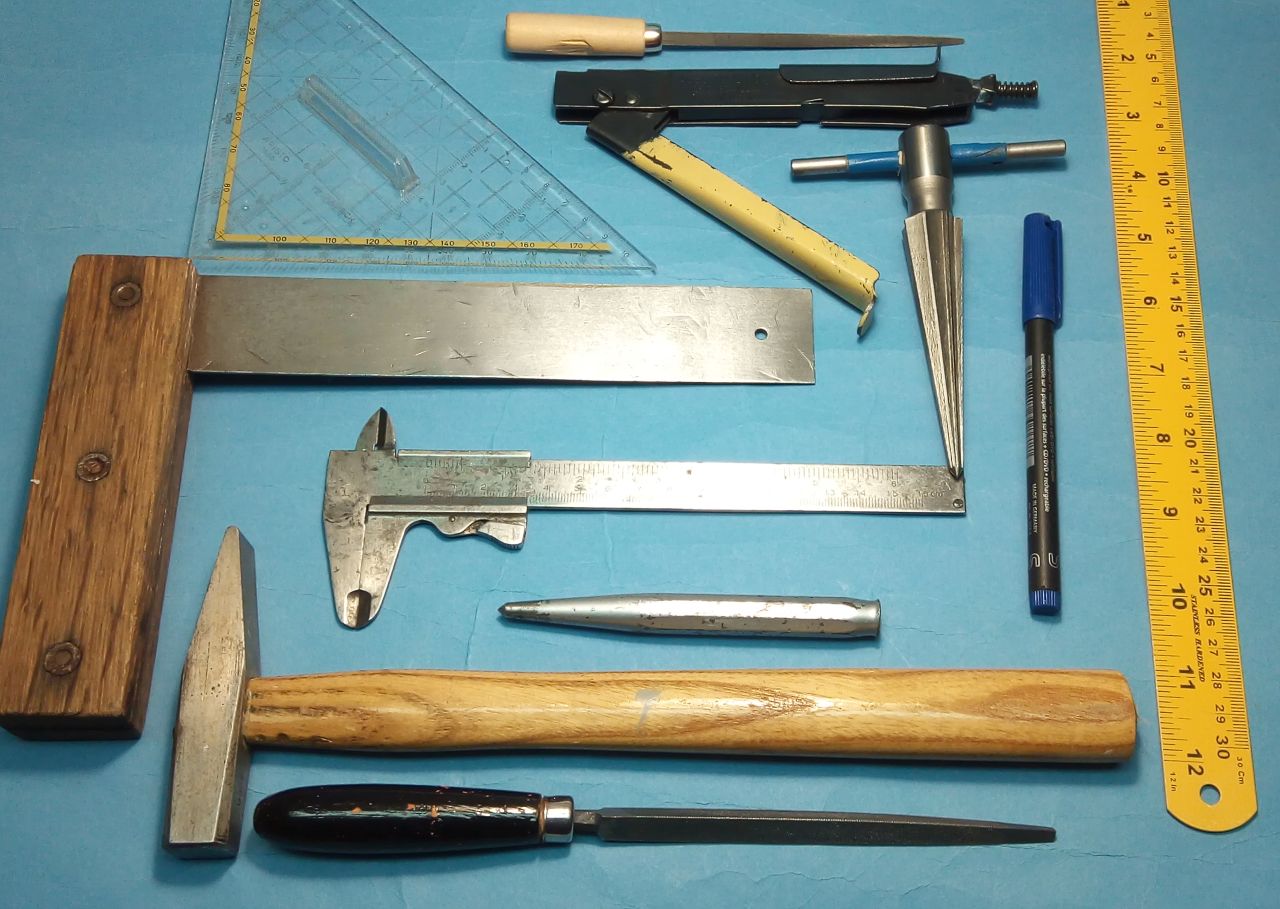
Ein Tipp zum genaueren Ankörnen: Nur durch das Ankörnen kann der Spiralbohrer nicht wegrutschen. Allerdings ist es nicht so einfach beim Ankörnen genau die Position zu treffen. Deshalb ist es ratsam mit einer Anreißnadel die genaue Position in das Blech von Hand einzudrücken. Dann hat mein eine winzige Delle, die als Führung für den Körner dient. Man haut dann beim Ankörnen nie mehr daneben.
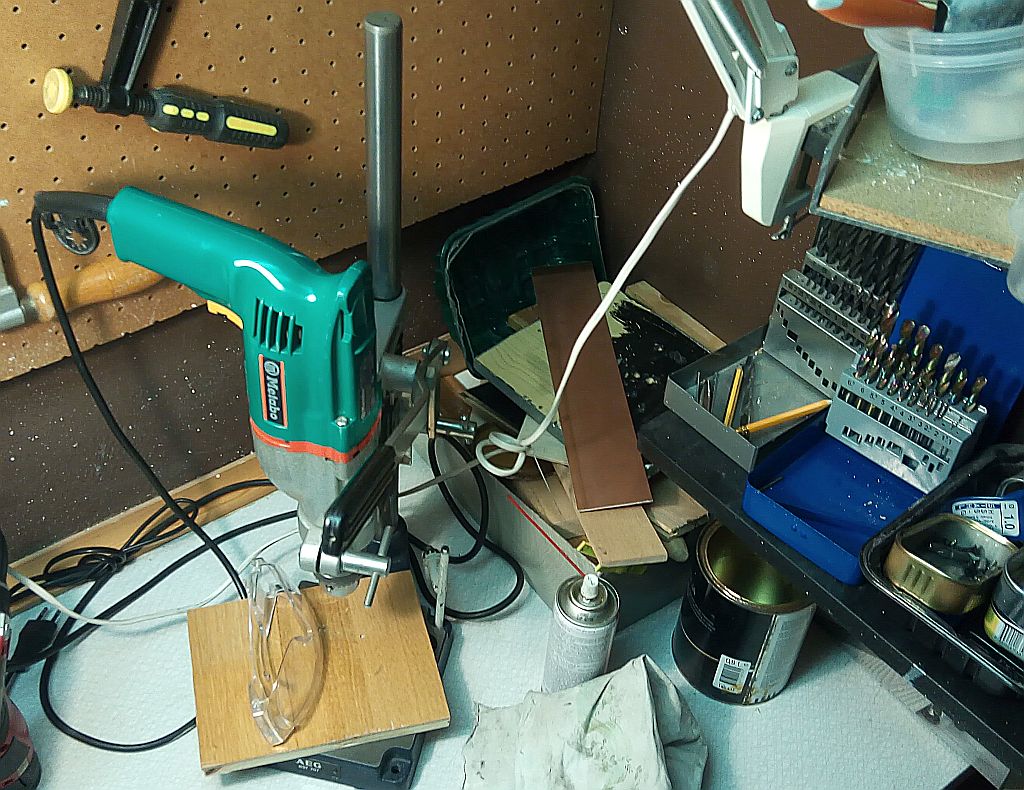
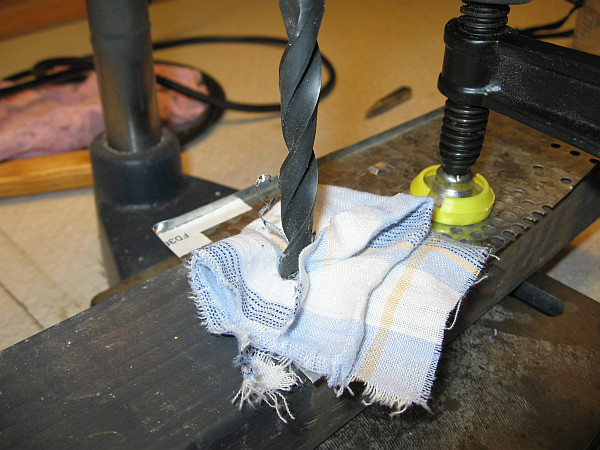
Schließlich ist helles Arbeitslicht von verschiedenen Seiten wichtig für die Genauigkeit.
Zum Schmieren und Kühlen der Bohrer kommt für Aluminium Brennspiritus zum Einsatz, für Stahl eignet sich Motoröl oder Rostlöser. Das Aluminium kann anschließend noch mit Autolackreiniger (Rubbing) poliert werden. Stahlblech muss wegen des Aussehens meistens lackiert werden. Matter Lack aus der Spraydose lässt Fehler und Unebenheiten des Bleches weniger gut erkennen. Lackierfehler können mit 1000er-Schleifpapier durch einen Nassschliff und Rubbing (eine schleifende Polierflüssigkeit für Autolack) behoben werden.
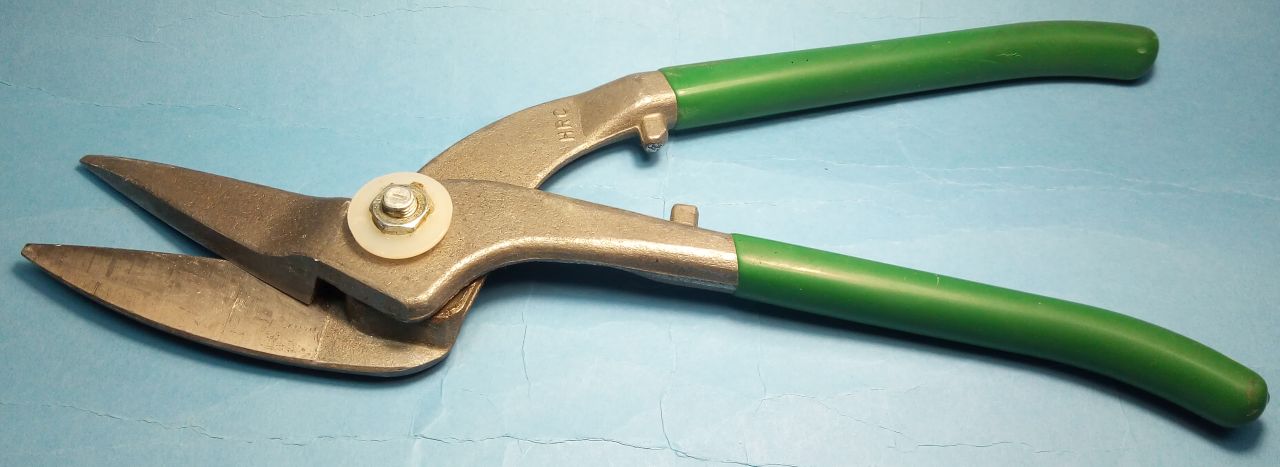
Die beiden nachfolgenden Videos erklären den richtigen Umgang mit verschiedenen Blechscheren, die es in verschiedenen Ausführungen gibt, wobei der Schwerpunkt auf Figurenblechscheren liegt. Dabei kommt es darauf an, auf welcher Seite das Abfallstück liegt und ob man die Schere unterhalb oder oberhalb des Blechs hält. Die richtige Handhabung ist in den nachfolgenden Videos vorgestellt, damit man schöne glatte und gerade Schnitte erhält ohne das als Werkstück dienende Blech zu verbiegen.
Der richtige Umgang mit „roten“ und „grünen“ Figurenblechscheren von einem Vollprofi erklärt. Laut diesem Video benötigt man nicht die „gelbe“ Figurenblechschere.
Handhabung einer Figurenblechschere
Video: Wie halte ich die Blechschere, damit sich das Blech nicht an der Schnittkante nicht verbiegt? Gut erklärt aber leider auf Englisch.
Im nachfolgenden Beispiel kommt 1 mm dickes Aluminiumblech zum Einsatz. Mit einer Durchlaufblechschere lässt es sich leicht in die passende Größe schneiden. Zum Anreißen verwende ich dünnen Filzstift und ein Geodreieck. Damit der Filzstift hält, muss das Aluminium manchmal mit Schleifpapier angeraut werden. Beim Anreißen und Schneiden muss man sich vorher festlegen, welche Seite des Strichs, der eine gewisse Dicke hat, maßgeblich ist.
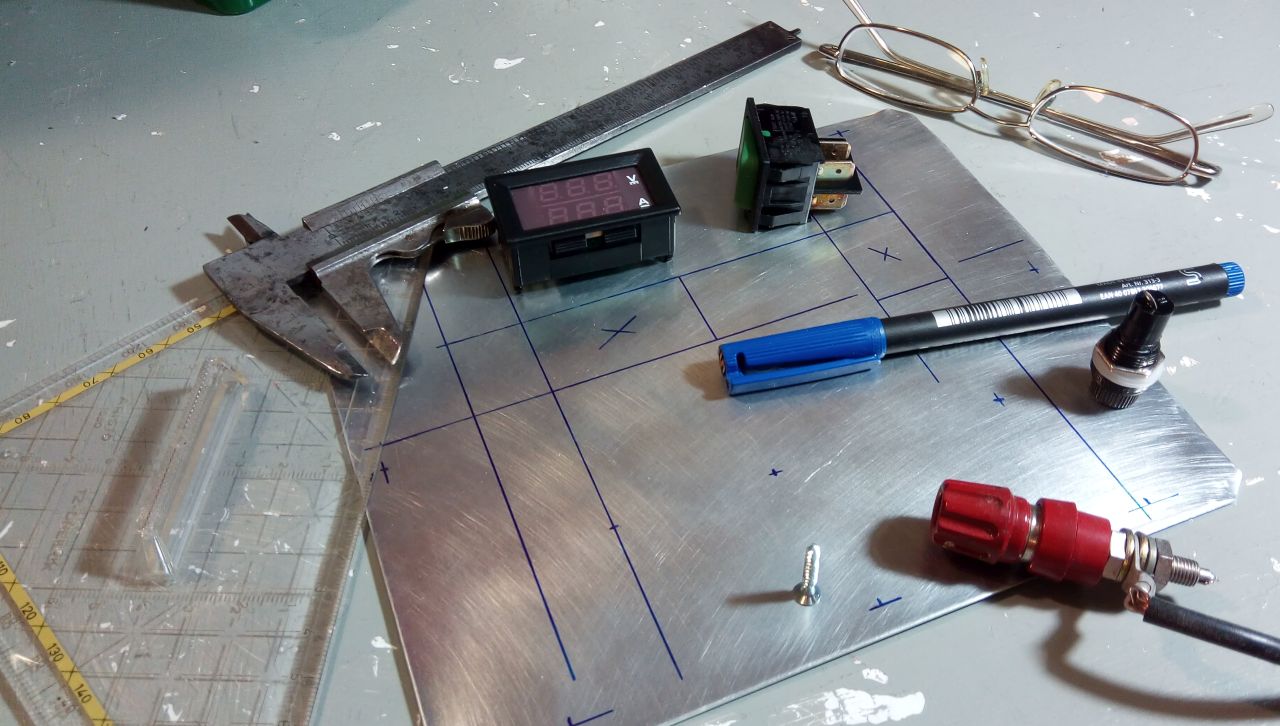
Hat man nun die Frontplatte im rechten Winkel und passender Größe vor sich, kommt der entscheidende Teil der Arbeit, der über Erfolg oder Misserfolg entscheidet: Das Anreißen oder Einzeichnen der rechtwinkligen Linien für die genaue Position der Bohrungen und Durchbrüche. Für diese Arbeiten haben sich Schieblehre, Geodreieck und ein dünner Filzstift bewährt. Bohrungen sind noch relativ einfach zu positionieren.
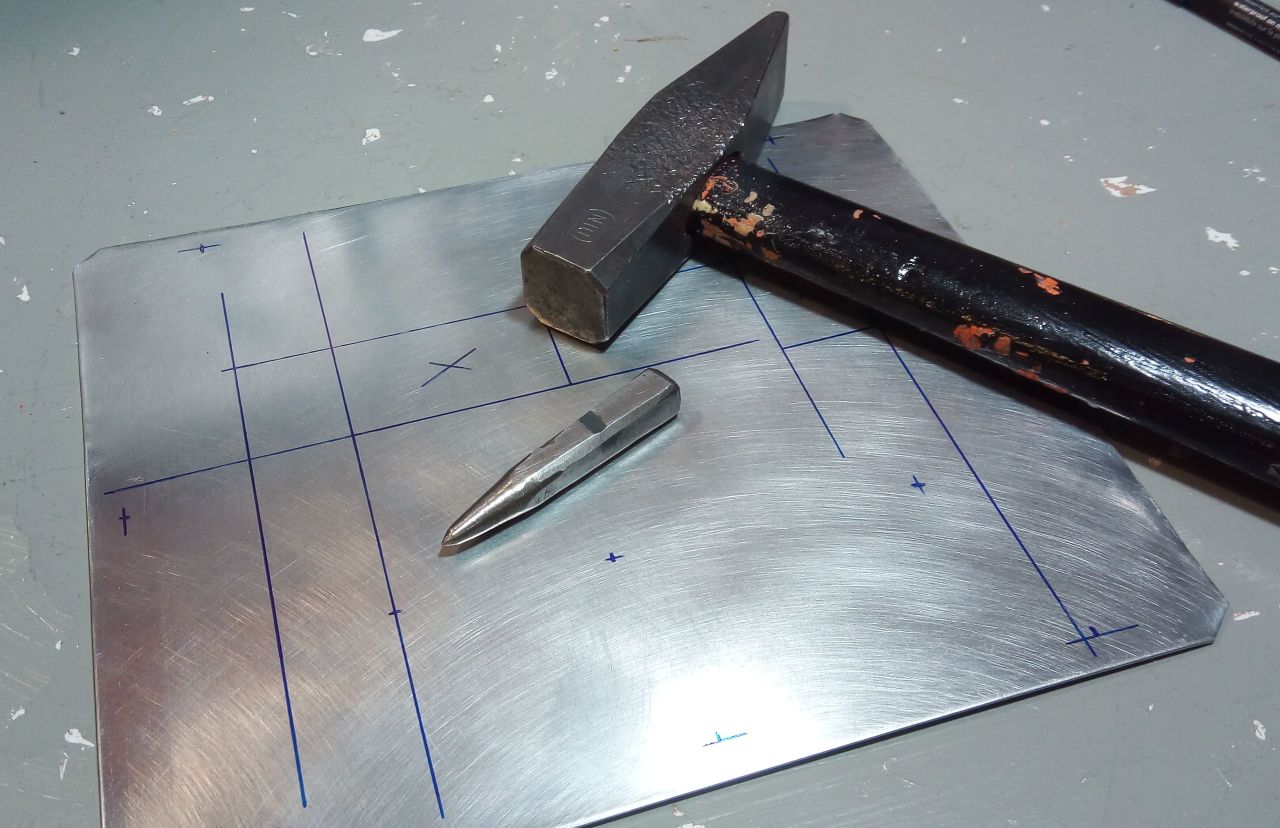
Schwieriger sind rechteckförmige Aussparungen für Schalter und Anzeigen mit Schnappbefestigungen. Um auf ein Zehntel mm genau die Linien zeichnen zu können, reicht das Geodreick alleine nicht aus. Es ist noch die Schieblehre zu Hilfe zu nehmen, um genau zu erkennen, wie die parallelen Linien zu ziehen sind. Dazu ist der Dorn für die Tiefenmessung hilfreich. Hier sollte man sich darauf einigen, dass beim Bearbeiten mit der Knabberzange als Markierung die inneren Kanten des Striches Gültigkeit haben. Um die Knabberzange ansetzen zu können, muss genau in der Mitte eine Markierung für den Bohrer gesetzt werden, die anzukörnen ist. Die Bohrung muss dann meistens noch mit der Reibahle aufgeweitet werden.
Wenn die Frontplatte nur kreisrunde Löcher benötigt, muss man nicht ganz so genau arbeiten. Dann reicht es alle Positionen der Bohrungen auf kariertes Papier aufzuzeichnen. Dieses Papier klebt man dann dann mit Klebeband auf das Blech. Dann lassen sich die Positionen mit dem Körner auf das Blech übertragen. Man schlägt also den Körner durch das Papier auf das Blech. Sollte man doch noch eine rechteckige Aussparung benötigen, sollte man diese wie bereits beschrieben direkt auf das Blech einzeichnen.
Zum Bohren existieren unter
https://elektronikbasteln.pl7.de/bohren-in-der-hobbyelektronik und
https://elektronikbasteln.pl7.de/kreisrunde-loecher-in-bleche-mit-dem-stofffetzentrick
Anleitungen.
Empfehlenswert ist immer das Ankörnen und Vorbohren und Schmieren. Mit hoher Drehzahl und geringem Vorschub gelingen kreisrunde Bohrungen ohne Grate. Die Grate lassen sich mit einem größerem Bohrer entgraten.
Nach dem Bohren und dem Erzeugen der Aussparungen lassen sich nun mit Schleifpapier oder mit Stahlwolle die Blechkanten entgraten, damit sie nicht mehr scharfkantig sind.
Die 4 Ecken des Blechs habe ich mit der Blechschere abgeknipst und dann rund gefeilt. Anschließend erfolgt mit Schleifpapier oder Stahlwolle das Entgraten. Zum Schleifen verwende ich neben 600er- bis 1000er-Schleifpapier zusätzlich Wasser und Seife. Schleift man zum Schluss immer in eine Richtung, erhält man ein harmonische Struktur der Oberfläche. Anschließend kann das Aluminium noch mit Polierpaste für Autolack oder mit Chromglanz zum Einsatz kommen. Es lassen sich mit der Polierscheibe spiegelglatte Aluminium-Oberflächen erzielen. Dann sind jedoch kleinste Unebenheiten erkennbar. Zum Schluss ist die Oberfläche mit Wasser, Seife, Spiritus oder Bremsenreiniger gründlich vom Schleifstaub und dem Schleif- oder Poliermittel zu reinigen. Die Grate und scharfen Kanten sind durch das Polieren und Schleifen verschwunden. Mit Stahlblech erhält man keine so schöne Oberfläche. Deshalb sollte man sie mit der Spraydose lackieren.
Alle Arbeiten lassen sich mit den gleichen Werkzeugen und Methoden mit Leiterplattenbasismaterial auf der Basis von Epoxid ausführen. Dieses Material lässt sich mit der Blechschere zuschneiden. Bei Pertinax geht dies nicht, denn es splittert und bricht beim Schneiden. Da das Epoxid-Material mit Glasfaser verstärkt ist sollte man es nicht sägen. Es macht die Sägen stumpf. Vom Sperrholz für die Frontplattengestaltung bin ich abgekommen, da es zu weich ist und die Schraubbefestigungen ausleiern.
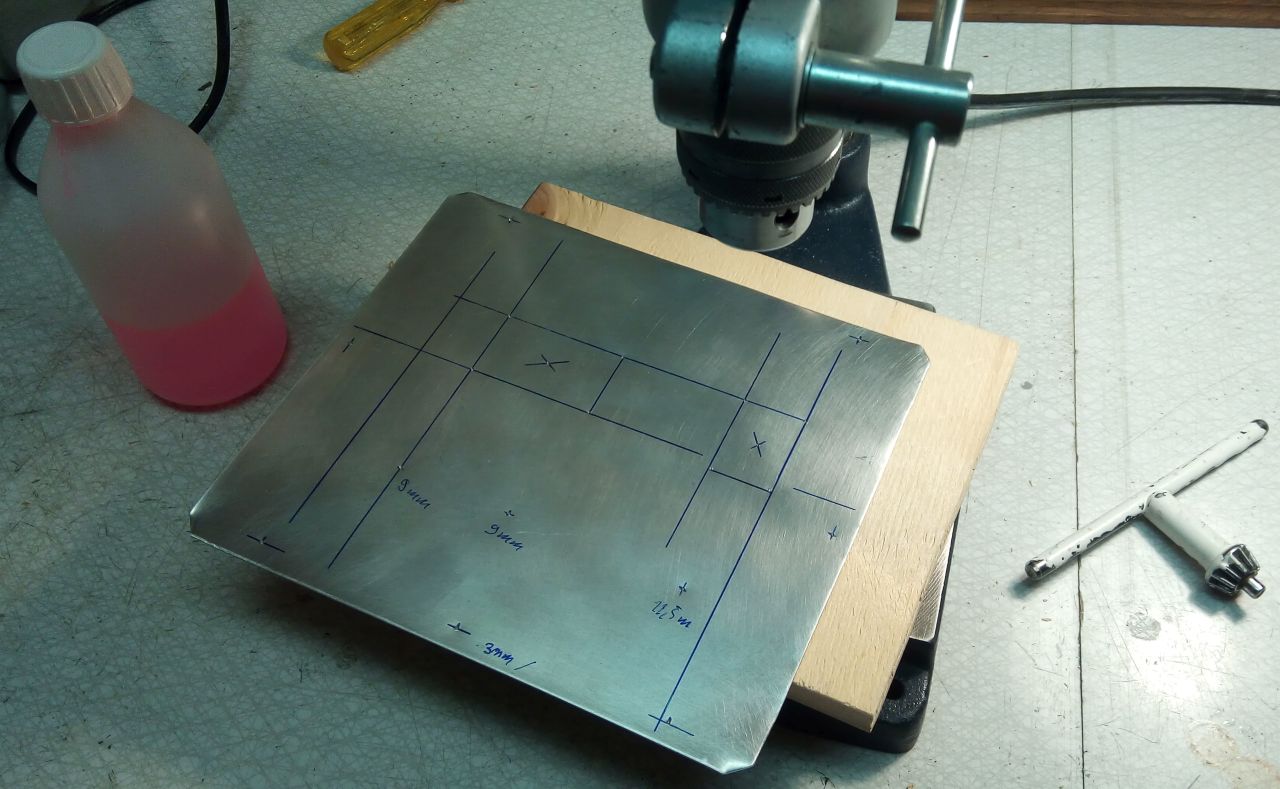
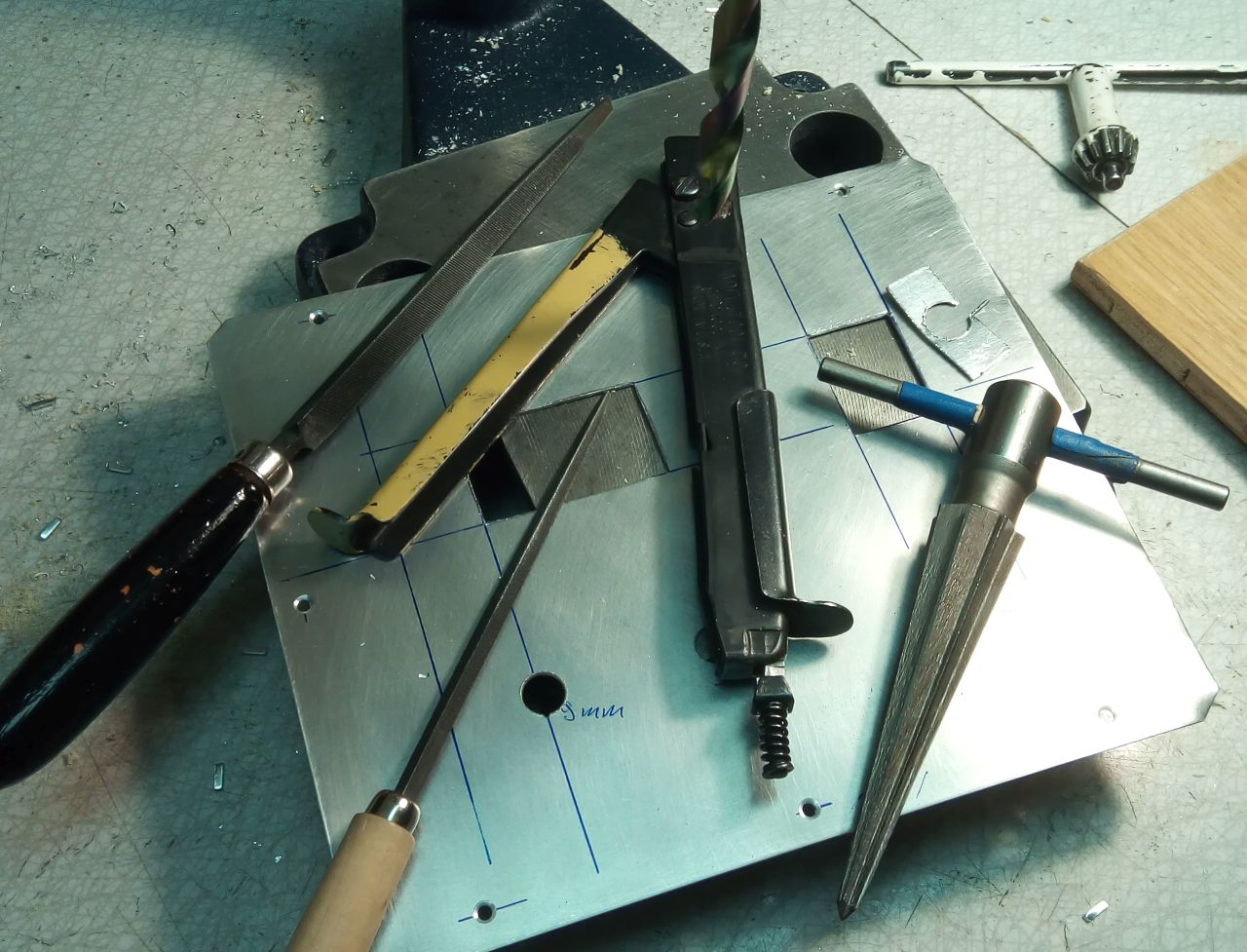
Video: Wie erzeugt man große Aussparungen in Blechen? Ein paar praktische Werkzeuge für die Blechbearbeitung im Einsatz. Das Video stellt auch diverse Knabberzangen (englisch = nibbler) vor. Handknabberzangen eignen sich gut für kleine rechtwinklige Durchbrüche wie sie in der Elektronik vorkommen. Das Video begreift man auch ohne ein Wort Englisch verstehen zu können.
Über den Umgang mit einer Knabberzange (handnibbler) für die Erzeugung rechteckförmiger Aussparungen im Blech. Es gehen übrigens auch runde Formen für z.B. Drehspulinstrumente oder Röhrenfassungen.
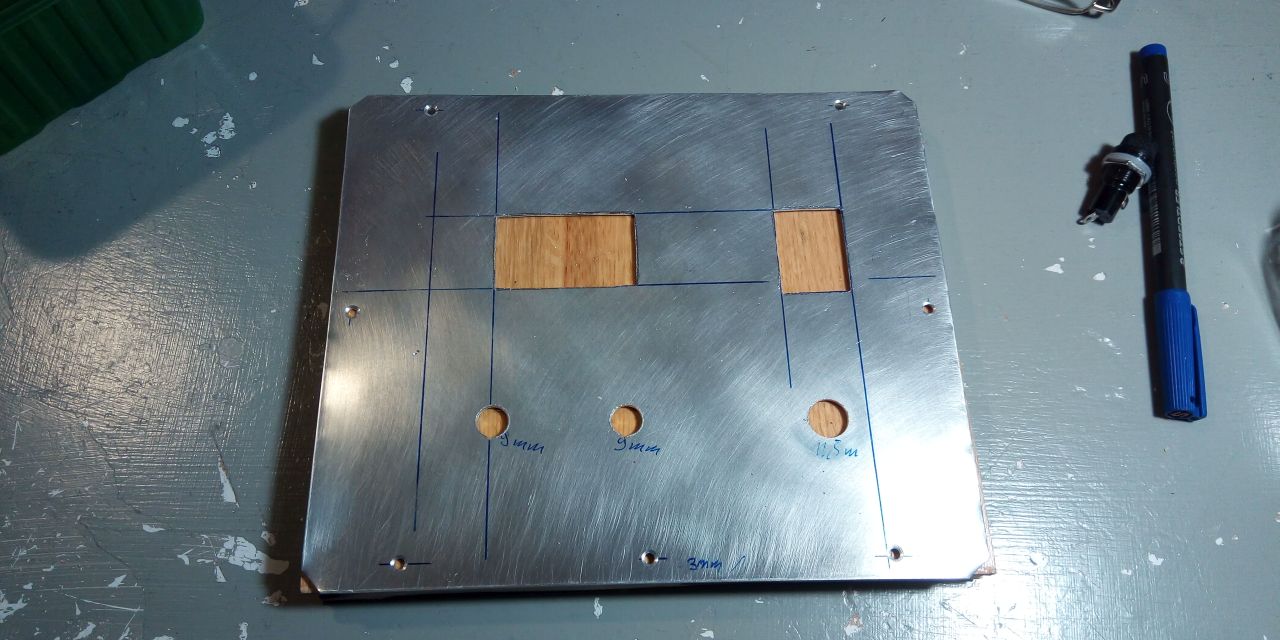
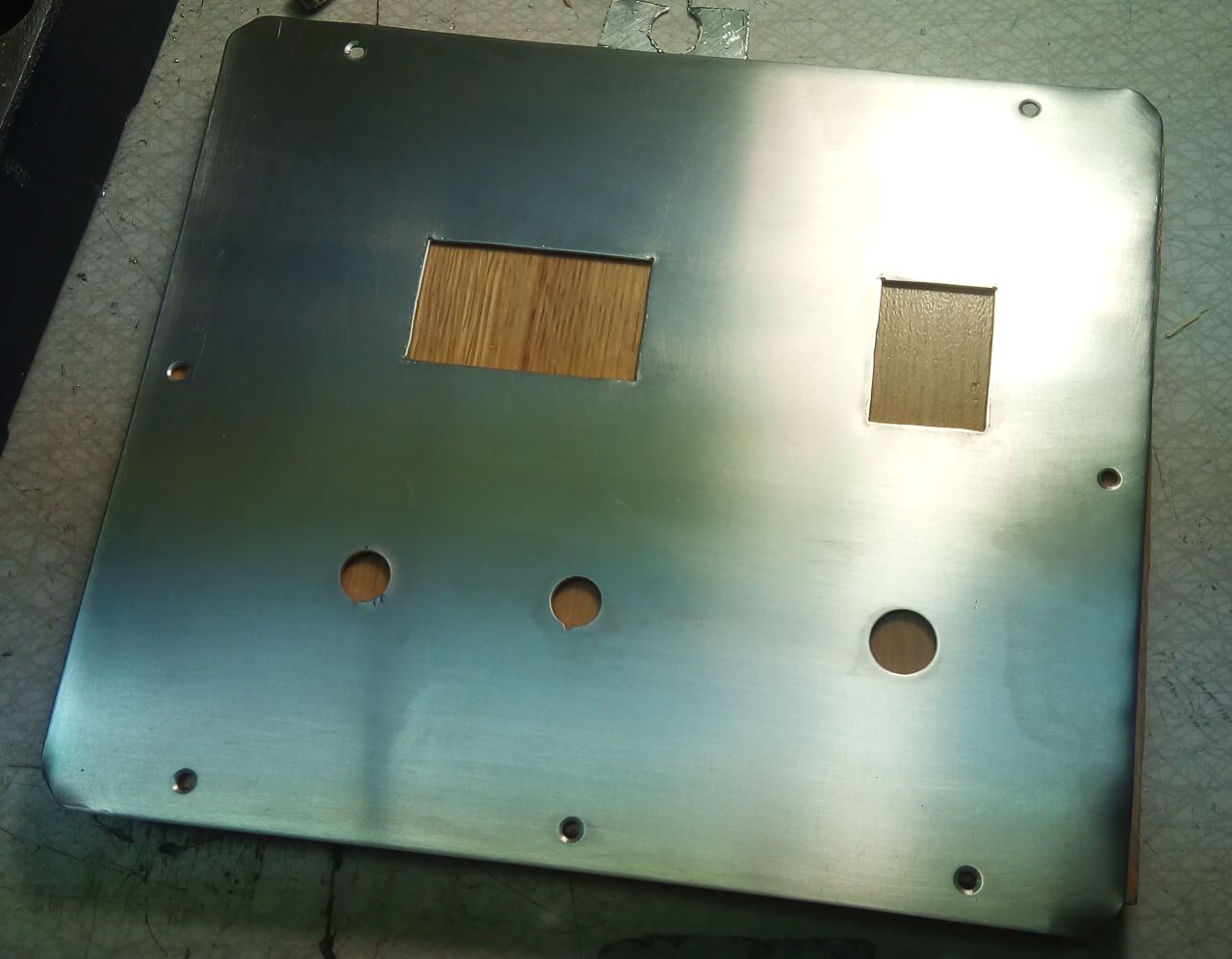
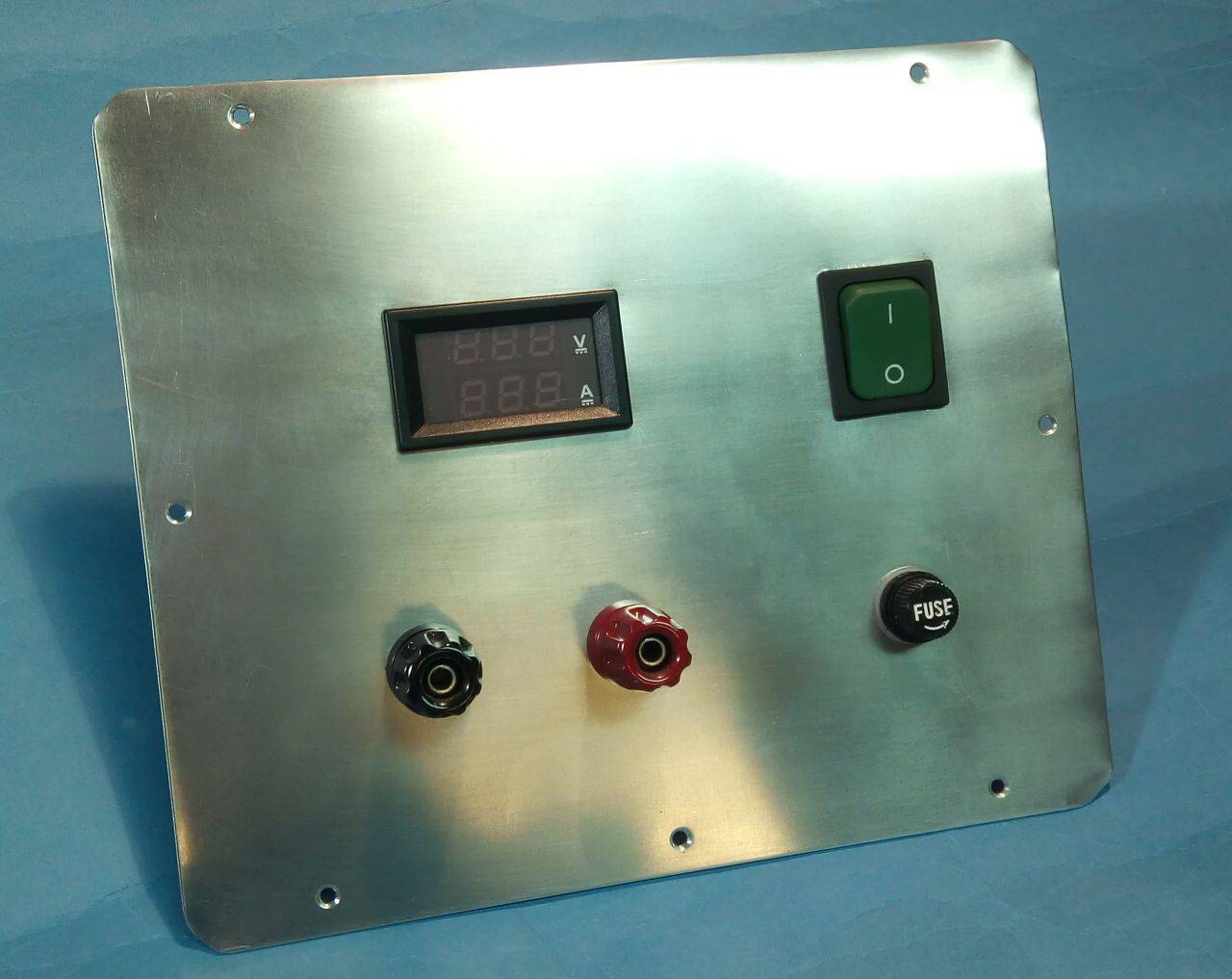
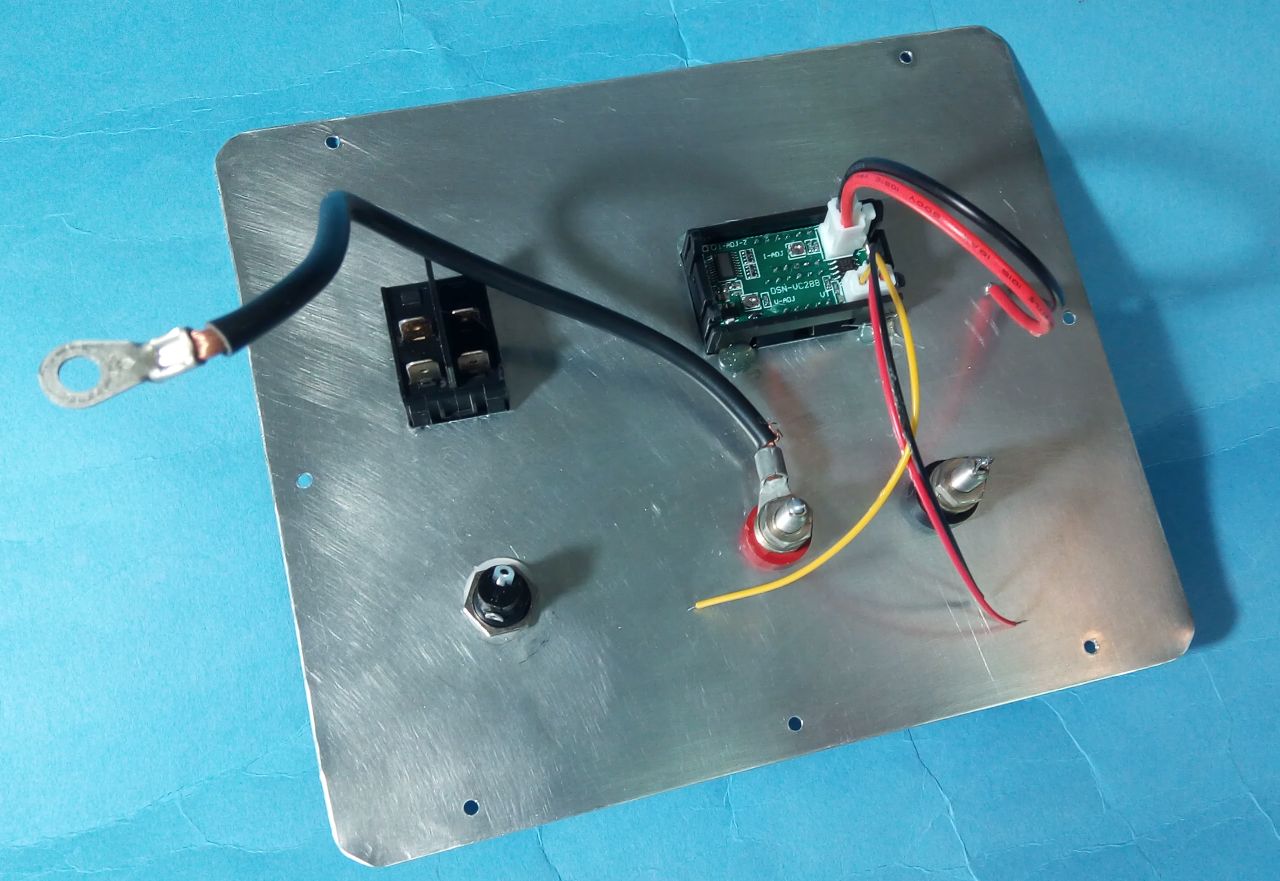
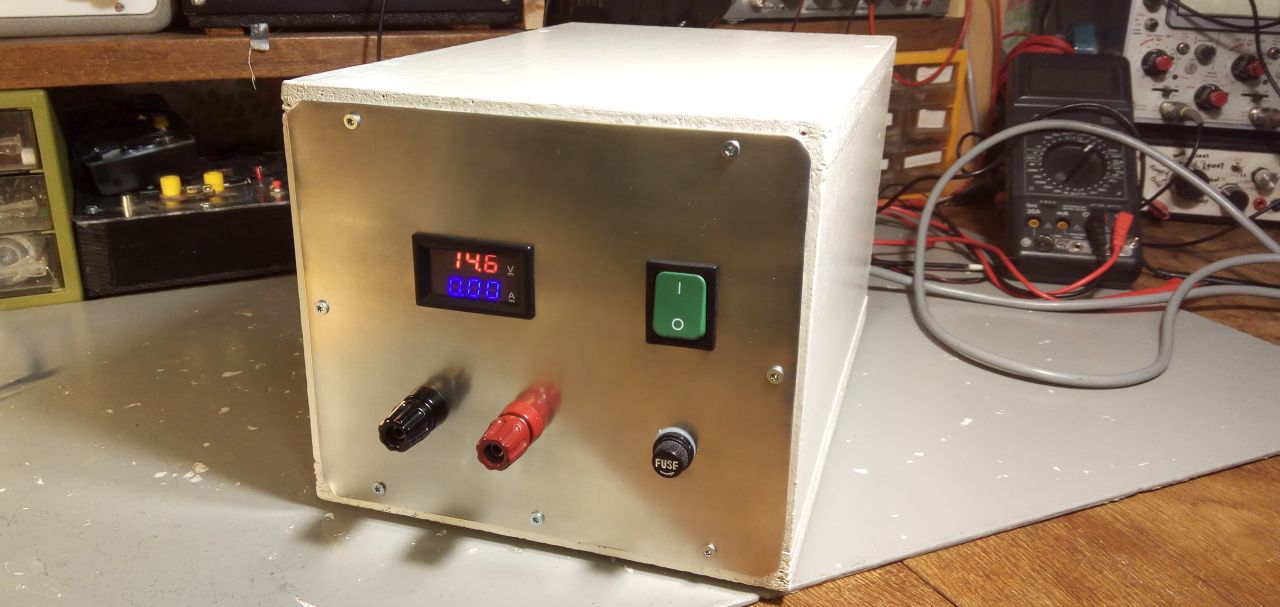
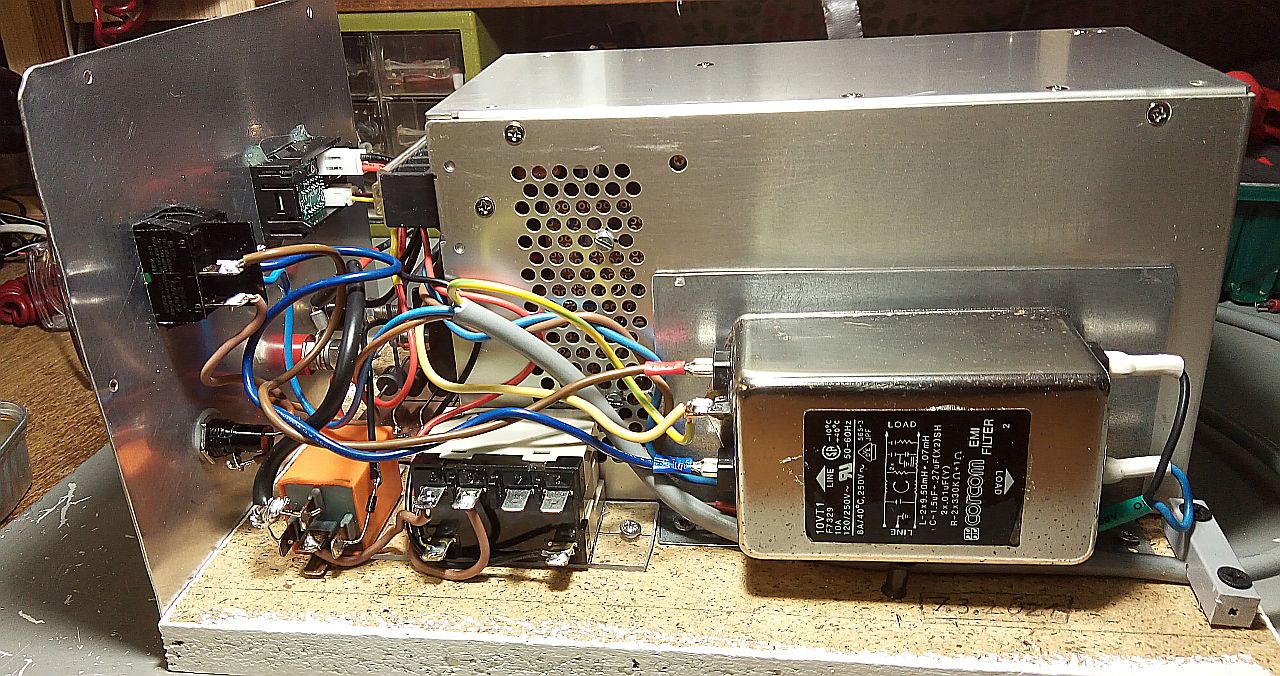
Für Stahlblech und Leiterplattenbasismaterial empfiehlt sich sich eine Lackierung mit der Spraydose. Das nachfolgende Video zeigt den richtigen Umgang mit der Lackspraydose. Sollte das Ergebnis nicht ganz perfekt aussehen, empfehle ich nach dem Trocknem noch einen Nassschliff mit 1000er-Papier und eine Politur mit einem groben Autolackreiniger (Rubbing):
Video über den richtigen Umgang mit Lackspraydosen
Klarlack aus der Spraydose richtig auftragen. Der Glanz des Aluminiums bleibt mit Klarlack besser erhalten.
Hier kann man sich einige Tricks von Profis abschauen, die mit einfachen Werkzeugen erstaunliche Dinge aus Blech herstellen:
Gewerbsmäßige Blechbearbeitung zur Herstellung von Herden, die mit Gas betrieben sind.
Eine andere Werkstatt, die mit Holz befeuerte Herde aus Blechen herstellt.